
When this process occurs, all three axes of your CNC move towards their maximum mechanical limit.
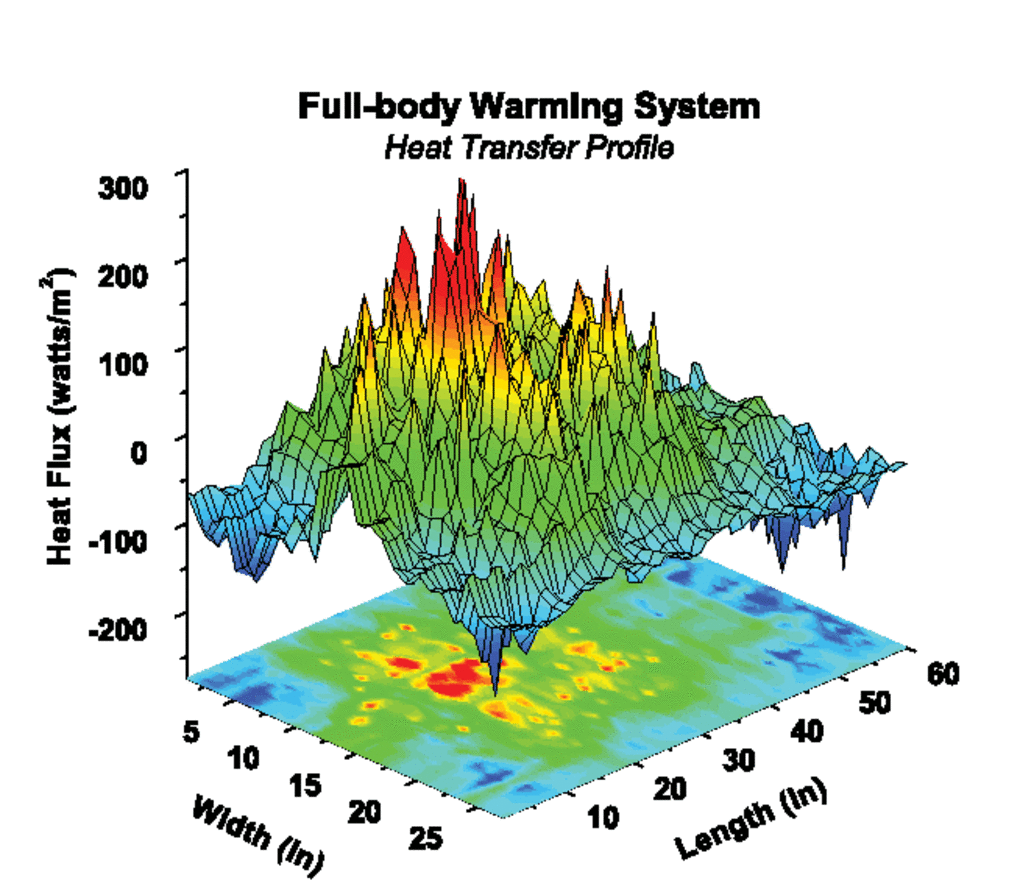
When your CNC first boots up, it has no idea where it is in physical space and requires a calibration to get its bearings. Check out the video below from Robert Cowan to see this in action:Įvery CNC machine has its own internal origin point called Machine Home. Understanding the difference between the movement of your tool and table is easier to show than explain with words. If reading that left you more confused than before, don’t worry. You are cutting into the piece which corresponds to a negative Z axis coordinate. Increasing the Z axis coordinate would move the spindle up, decreasing it would move it down into a workpiece. For example, increasing the X coordinate value moves the table left, but looking from the perspective of the tool, it’s moving right along a workpiece. The movement of your CNC along the coordinate system is always based on how your tool moves, not the table. If only it were as simple as shoving a block of metal into your CNC and pressing go. To do this, the machine needs to understand the position of the stock in physical space. However, something like a milling machine has to subtract material away from an external object.
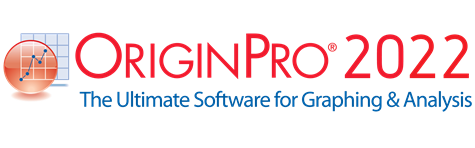
There’s no question about where the piece starts on the build plate. Why Do Coordinates Matter for CNC Milling?Īdditive machines build a part from the bottom up. In this article, we’ll be covering the basics of the CNC coordinate system, including the Cartesian coordinate system, work coordinate system (WCS), and offsets. The technology might change, but the fundamentals remain essentially the same. Even the latest CNC machines are the same at their core: they use an X, Y, and Z-axis to define the coordinate space inside the machine, and a tool (sometimes an endmill, sometimes an extruder, sometimes a laser beam) moves around that space.
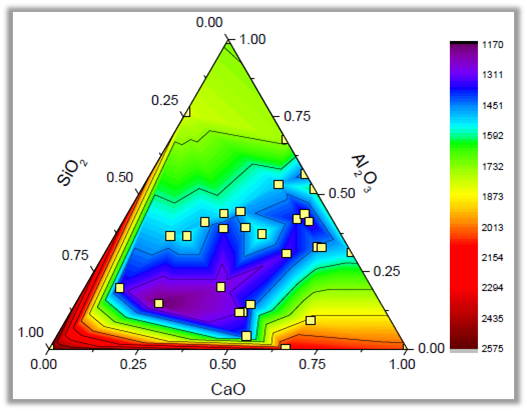
Sources: Press materials received from the company and additional information gleaned from the company’s website.You’ll use your CNC milling coordinate system fundamentals everywhere, not just for one particular CNC machine. OriginPro contains all of the Origin 9.1 features, as well as new tools for Partial Least Square Regression, additional Power and Sample Size tests, an Orthogonal Distance Regression algorithm for nonlinear curve fitting, a tool to fit and rank multiple fitting models, and a gadget to perform 2D integration over a region of interest. New data analysis features include Akima Spline interpolation, Lowess and Loess smoothing, and several improvements to existing analysis tools.
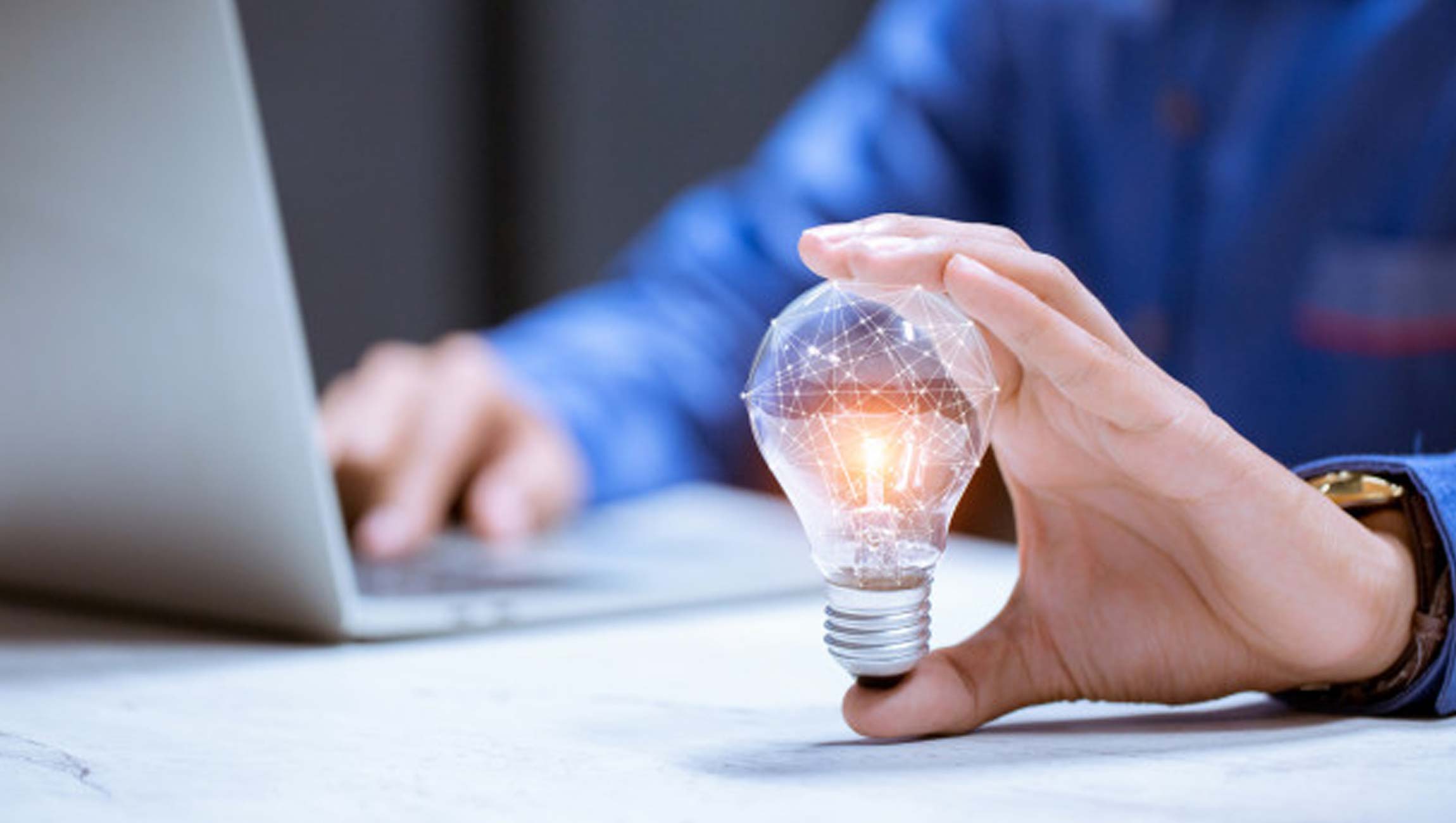
The latest version also introduces auto-positioning of labels in graphs, with the ability to add leader lines and to place labels arbitrarily such as attaching to data plot, to axes, or at fixed positions within the graph layer. The new tree-based graph axis dialog design provides a number of additional advanced options for graph customization, including multiple axis breaks with customizable break gaps and break indicators, user-defined axes scales, and tick label tables. Several time-saving features are also included, such as Batch Plotting to create duplicate graphs from other worksheets and columns, Batch Analysis on multiple data plots using interactive gadgets, copying and pasting analysis operations to new data, and a custom worksheet header row for quickly assigning and editing column formulas. New graph types include Grouped Box Chart and Column/Bar Plot, Piper Diagram, 3D Ternary Surface Plot, 3D Waterfall Plot, 100% Stacked Column/Bar Plot, and Marginal Histogram/Box Chart. OriginLab announced the release of Origin and OriginPro version 9.1.Īccording to the company, Origin 9.1 includes more than 200 new features and improvements.
